Metal Casting Types, Principles, Characteristics and Products
The metal casting and molding process (also known as liquid molding) refers to a molding method in which metal is melted by heat and cast into a pre-made mold (a container that turns the liquid metal into a solid casting). After solidification, a metal product with a certain shape and performance is obtained. Liquid molding is one of the earliest manufacturing processes, and although hundreds of years of casting history have demystified the process, it remains a fundamental molding technology. Casting has the characteristics of low production cost, high process flexibility, and strong adaptability. It is suitable for producing castings of different materials, shapes, and weights and suitable for mass production. The disadvantage is that the tolerance (maximum limit size minus the minimum limit size) is large, internal defects are prone to occur, and a lot of materials and equipment are required. At the same time, casting production will produce dust, harmful gases, and noise, causing pollution to the environment.
Casting Process
The casting process usually includes the following three stages: mold preparation, melting and pouring of the casting metal, and casting processing and inspection.
-
1. Casting mold preparation: Casting molds can be divided into sand molds, metal molds, ceramic molds, clay molds, graphite molds, etc. according to the materials used. According to the number of uses, they can be divided into disposable, semi-permanent, and permanent molds. In primary castings, the mold is usually destroyed during the removal of the casting, and its cavity is often made from a pattern made of wax, wood, plastic, or metal. A permanent cast is a more expensive but reusable cast. Because the cost is high and on-the-spot modifications are extremely expensive, and some are even unrepairable, it requires more design preparation time to prepare the mold. The quality of mold preparation is the main factor affecting the quality of castings;
-
2. Melting and pouring of cast metals: Cast metals (cast alloys) mainly include cast iron, cast steel and cast non-ferrous alloys;
-
3. Casting processing and inspection: Casting processing includes cleaning the core and foreign matter on the surface of the casting, removing the pouring riser, grinding burrs and seams and other protrusions, as well as heat treatment, shaping, anti-rust treatment, and rough machining.
Casting Type
There are many types of castings, which are customarily divided into ordinary sand casting and special casting according to the modeling method. Ordinary sand casting includes two categories: green sand mold, dry sand mold, and chemical-hardened sand mold. Special casting, according to the molding materials, can be divided into special castings with natural mineral sand and gravel as the main molding material (such as investment casting, shell casting, solid mold casting, ceramic mold casting, etc.) and metal as the main casting material. There are two types of special castings (such as metal mold casting, pressure casting, continuous casting, low-pressure casting, centrifugal casting, etc.).
Ordinary Sand Casting
Wet Sand Type and Dry Sand Type
Green sand molding compacts wet sand into a sandbox with two halves of a wooden or metal mold. The assembled casting can be with or without a core. The molten metal is poured into the final cavity and the parts are taken out. The mold will then be destroyed. The wet state moisture of the molding sand used for casting dry sand molds is slightly higher than that of the molding sand used for wet molds. After the sand mold is made, the surface of the mold cavity should be coated with refractory paint. The refractory material can prevent the sand from overheating, and then be placed in an oven to dry. After it cools, it can be molded and poured. Drying clay sand molds takes a long time and consumes a lot of fuel. Moreover, the sand molds are prone to deformation during the drying process, which affects the accuracy of the castings.
Chemically Hardened Sand Mold
The molding sand used in chemically hardened sand molds is called chemically hardened sand. The binder is generally a substance that can undergo molecular polymerization under the action of a hardener to form a three-dimensional structure. Commonly used are various synthetic resins and water glass.
The characteristics of the chemical hardening sand casting process are:
-
1. The casting mold can more accurately reflect the size and contour shape of the pattern, and the dimensional accuracy of the produced castings is high;
-
2. The equipment has a lightweight structure, low power, and high productivity, and the sand treatment work can be simplified;
Special Casting
Investment Casting
Investment casting is also called lost wax casting, precision casting, or monolithic casting. It is based on the final product, pressing paraffin materials into precise and smooth wax molds, coating multiple layers of refractory materials on the wax molds, waiting for the slurry to dry and harden to form a mold shell, and then the wax solidified in the mold shell is The mold is melted to make it flow out, and then the mold shell is baked to make it strong and dry. Finally, the molten liquid metal is poured into the mold shell. After the liquid metal cools and solidifies in the mold shell, it becomes a precise and smooth casting. Its casting is made of 70% to 80% gypsum and 20% to 30% reinforcing fibers. It is mainly used to produce steam turbine and gas turbine blades, pump impellers, cutting tools, and small parts for aircraft, automobiles, tractors, pneumatic tools, and machine tools.
Characteristics of Investment Casting:
-
1. Castings have high precision and good surface quality. For example, for investment casting turbine engine blades, the casting accuracy has reached the requirement of no machining allowance;
-
2. Castings with complex shapes can be manufactured. Complex components composed of several parts can be cast in one go by investment casting;
-
3. The types of casting alloys are not limited and can be used for high melting point and difficult-to-cut alloys, which have significant advantages;
-
4. The production batch size is basically unrestricted, and it can be produced in batches and large batches, as well as single pieces and small batches;
-
5. The process is complicated, the production cycle is long, and the production cost is high. The castings should not be too large or too long.
Shell Casting
Shell casting is a casting method that uses thin shell molds to produce castings. The process is to use a type of heat-hardened molding sand (usually resin sand) to cover the heated metal mold (heating temperature is generally about 300°C) plate, so that it hardens into a thin shell, and the thickness of the thin shell is generally 6~ 12mm, has sufficient strength and rigidity, so after the upper and lower mold shells are clamped with clamps or glued with resin, the casting mold can be formed and the casting can be poured without a sandbox.
Shell casting has the following characteristics:
-
1. It can significantly reduce the amount of molding sand used;
-
2. The obtained castings have clear outlines, smooth surfaces, and precise dimensions, and can be processed without mechanical processing or with only a small amount of processing. It is especially suitable for the production of castings of various alloys with large batches, high dimensional accuracy requirements, thin walls, and complex shapes;
-
3. The resin used in shell casting is expensive, the template must be precisely processed, and the cost is high. It also produces a pungent smell during pouring, which to some extent limits the wide application of this method.
Solid Casting
Full mold casting uses a polystyrene foamed plastic pattern to replace the ordinary pattern. After the mold is made, molten metal is poured in without taking out the pattern. Under the action of the molten metal, the plastic pattern burns, vaporizes, and disappears, and the molten metal replaces the original plastic. The spatial position occupied by the mold is used to obtain the required casting after cooling and solidification.
Real mold casting has the following characteristics:
-
1. Due to the use of foam plastics that vaporize when exposed to molten metal, there is no need for mold removal, no parting surface, and no core, so there is no flash or burr;
-
2. Castings with various complex shapes can be bonded and formed into a whole using foam plastic molds, which reduces processing and assembly time, reduces casting costs by 10% to 30%, and provides sufficient freedom for casting structural design;
-
3. The casting production process is simplified, the production cycle is shortened, and the molding efficiency is 2 to 5 times higher than that of sand casting;
-
4. The solid casting pattern can only be used once, and the foam plastic has low density and low strength. The pattern is easily deformed, which affects the dimensional accuracy of the casting, and the gas generated by the pattern during casting pollutes the environment.
Pressure Casting
Pressure casting is a casting method in which liquid or semi-liquid metal fills the mold at high speed under high pressure and solidifies into a casting under pressure. The pressure used is 4~500MPa, and the metal filling speed is 0.5~120m/s. The die-casting machines used for pressure casting are divided into two types: hot-pressure chamber die-casting machines and cold-pressure chamber die-casting machines. The hot press chamber die-casting machine is suitable for die-casting lead alloy and zinc alloy castings with low melting points, and can also be used for die-casting magnesium alloy castings. Cold press chamber die casting machine is suitable for die casting aluminum alloy, copper alloy, or magnesium alloy castings. Ordinary die castings have many pores and are difficult to heat treat and weld, which affects their performance. Therefore, several special pressure casting methods are mostly used in production. Commonly used ones include vacuum die casting, inflatable die casting and precision die casting.
-
1. Vacuum die casting: During die casting, the air in the mold cavity is removed in advance;
-
2. Inflatable die casting; during die casting, the casting cavity is first filled with oxygen, so that the liquid metal and oxygen form solid oxide, which is dispersedly distributed inside the casting;
-
3. Precision die casting: Liquid metal fills the mold cavity at low speed. After the metal fills the cavity, a small piston is used to add pressure.
Pressure casting can produce castings with complex shapes and can effectively save materials, energy, and processing hours. The weight of die castings ranges from a few grams to tens of kilograms. The pressure casting method is suitable for mass-produced castings. It has high production efficiency and is easy to mechanize and automate the production process. It is widely used in manufacturing industries such as automobiles, instruments, agricultural machinery, electrical appliances, and medical equipment.
Continuous Casting
Continuous casting is a casting method that uses a penetrating crystallizer to continuously pour liquid metal into one end and continuously pull out the molding material from the other end. Crystallizers are generally made of materials with good thermal conductivity and certain strength, such as copper, cast iron, graphite, etc. The cast molding materials include square, rectangular, round, flat, tubular, or various special-shaped cross-sections.
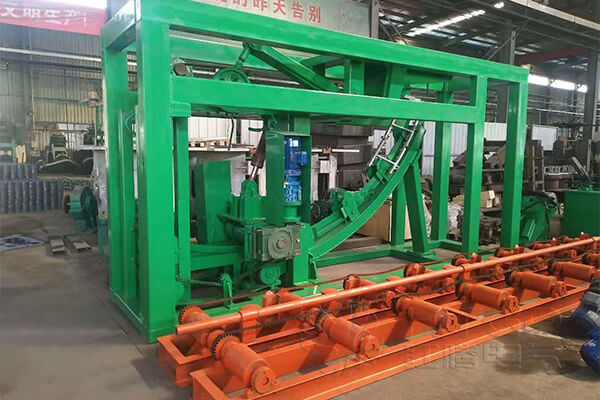
This is a schematic diagram of a horizontal continuous cast steel ingot. The crystallizer is at the bottom of the molten steel ladle. The molten steel is continuously pulled out into ingots through the crystallizer. The surface-solidified ingot is completely solidified by secondary cooling by sprayed water below the crystallizer. When the ingot is pulled to a certain length, it is cut into sections by a cutting machine for further processing.
Characteristics of continuous casting
-
1. Suitable for the production of castings of iron, steel, copper, lead, magnesium, and other alloys with constant cross-sectional shapes and large lengths;
-
2. The equipment and processes used in continuous casting are very simple, and the production efficiency and metal utilization rate are high. When used to form a production line with a rolling mill, it can also save a lot of energy.
Overview
Casting production lines play a vital role in the foundry industry. From the classification of production lines to the introduction of application fields, this article hopes readers can have an in-depth understanding of the role and value of casting production lines.