How to Avoid Bending of Rolled Bars in Rolling Mill?
In the field of metal pressure processing, hot rolling causes plastic deformation of the metal through a rolling mill above the metal’s recrystallization temperature. The hot rolling process generally includes heating of raw materials, rolling of raw materials, cooling of finished products, and segmented packaging of finished products. Bar is a product of hot rolling. During the hot rolling process, bending will occur. Even after later straightening, it still cannot meet the requirements, resulting in batches of waste products.
Causes of Bar Bending During Rolling
Generally, the reasons for the bending of rolled parts are uneven cooling speed and inconsistent shrinkage during hot rolling; uneven heating temperature of raw materials; improper installation of rolling mill accessories during hot rolling, etc. At present, wire bar rolling control bending generally adopts online real-time control during the rolling process, such as adjusting the inlet and outlet guide devices of the rolling mill and optimizing the pass pressure configuration. However, due to the uneven temperature of the blank, the temperature difference between the head and the tail, and the uneven wear of the hole, the final control effect is not obvious.
Solution
There is a way to avoid bending of the bar during rolling. This method coordinates the design of billet heating, rolling temperature control, cooling bed cooling temperature control, and sawing and finishing of the bar, so that the easily bendable bar can effectively avoid the bending, avoid the surface hardening phenomenon caused by bending and straightening of bars, and meet the needs of users. Specific steps are as follows:
Billet Heating
Put the continuous casting billet (260mm) into the heating furnace for heating. The temperature of the preheating section is 500~950℃, the temperature of the heating section I is 950~1120℃, the temperature of the heating section II is 1120~1210℃, and the temperature of the soaking section is 1130~1180℃, soaking section holding time≥35 minutes, total heating time≥210 minutes; continuous casting billet section temperature difference <30℃.
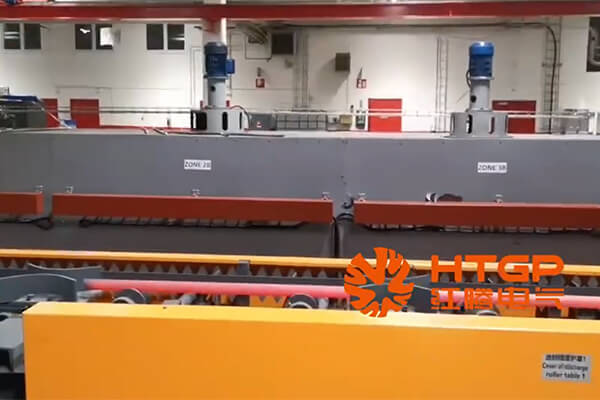
High-pressure water dephosphorization
After the continuous casting billet comes out of the furnace, it enters the high-pressure water dephosphorization device with a water pressure of 25 MPa to remove the iron oxide scale on the surface of the continuous casting billet.
Rough Rolling
The roughing rolling temperature is controlled at 1050°C, and the continuous casting billet enters the rough rolling unit. The rough rolling mill unit has a total of 7 rolling mills. The rolling mill type is a high-stiffness short-stress line rolling mill with an alternating horizontal and vertical arrangement. After rough rolling, it is sheared by a hydraulic head.
Intermediate Rolling
After rough rolling, the continuous casting billet enters the intermediate and finishing rolling unit. The intermediate and finishing rolling mill unit consists of 6 rolling mills.
Finish Rolling
After intermediate rolling, the continuous casting billet enters the finishing rolling unit. The temperature after finishing rolling, that is, the final rolling temperature, is controlled at 900 to 950°C;
Cooling Bed Cooling
The bars obtained after finishing rolling enter the double-scale cooling bed for cooling, where the bars are arranged on the cooling bed at intervals of 2 to 3 tooth pitches; the temperature of the upper cooling bed is≤920℃, and the temperature of the lower cooling bed is≤350℃.
Bar Sawing
The bars are sawed and segmented, collected and bundled and then sent to the slow cooling pit for slow cooling. The entering temperature is between 240°C and 300°C. The bars are fully slow cooled in the slow cooling pit for 24 hours, and the exit temperature is≤100℃.
Bar Finishing
After straightening, peeling, and flaw detection, the bars are packaged in a standardized manner.