A Comprehensive Guide to Induction Furnace Coil Cooling Systems
Induction furnace coil cooling systems play a crucial role in maintaining the performance and longevity of induction furnaces. These systems are designed to remove excess heat generated during the melting process and ensure optimal operating conditions. Generally, we can divide the induction furnace coil cooling systems into three types, closed water cooling system, open water cooling system, and air cooling system. In this comprehensive guide, we will explore the components, working principles, and features of induction furnace coil cooling systems.
Components of Induction Furnace Coil Cooling Systems
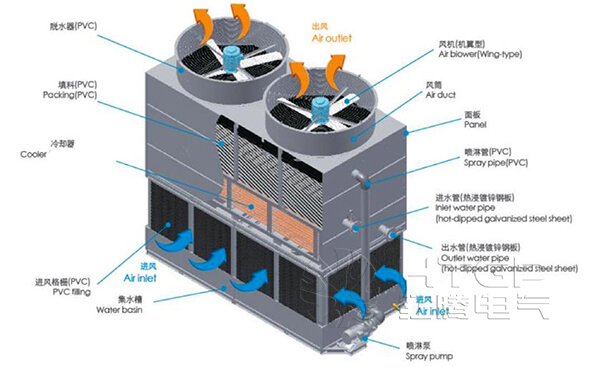
Water Circulation Pump
Responsible for circulating the cooling water through the coil. It ensures the pressure of the cooling water flowing into the induction furnace coil.
Spray system
Uses a large-flow basket-type nozzle to ensure continuous and even spraying of water on the coil surface.
Heat Exchanger
Transfers the heat from the cooling water to another medium, such as air or a separate water loop.
Air Intake Grille
Made of corrosion-resistant PVC, the dual-channel design prevents and reduces the formation of algae inside the unit.
Control System
Monitors and regulates the temperature, flow rate, and pressure of the cooling water.
Working Principles of Induction Furnace Coil Cooling Systems
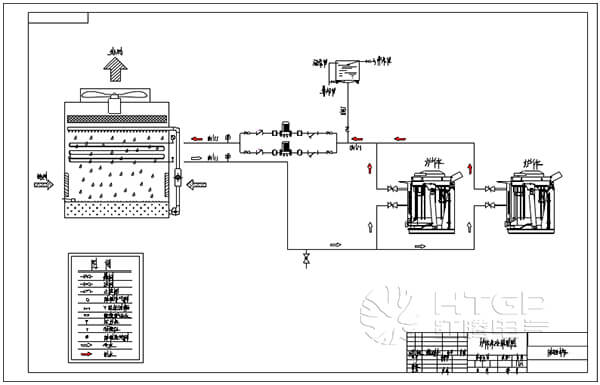
Induction furnace coil cooling systems are commonly used to maintain the temperature of the coil and prevent overheating during the melting process. These systems play a crucial role in ensuring efficient and safe operation of the induction furnace. Let’s explore the working principles of closed water cooling systems in induction furnaces.
Circulation of Cooling Water
The closed water cooling system consists of a network of pipes, valves, and a pump that circulates cooling water throughout the system. The cooling water absorbs heat from the coil and is then cooled down before being recirculated. The circulation of water allows for efficient removal of heat from the coil.
Water Supply and Return
The cooling system is connected to a water supply source, such as a cooling tower or a chiller unit. The water supply is responsible for providing a continuous flow of cooling water to the system. After absorbing heat from the coil, the heated water is returned to the cooling tower or chiller unit for cooling before being recirculated.
Heat Transfer
The heat transfer process occurs as the cooling water comes into direct contact with the hot coil. The water absorbs the heat generated by the induction process, thereby cooling down the coil. This heat transfer mechanism helps maintain the coil at an optimal temperature and prevents it from overheating.
Heat Exchange
After absorbing heat from the coil, the heated water is directed to a heat exchanger. The heat exchanger acts as a heat dissipation unit, where the heat from the water is transferred to the surrounding environment, typically through air or another water loop. This process helps bring the temperature of the cooling water back down before it is recirculated.
Applications
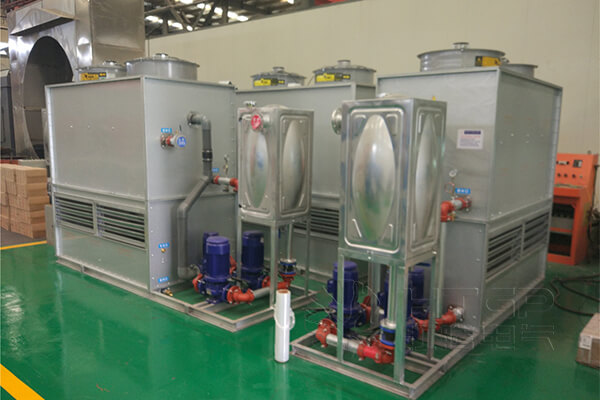
It is suitable for all kinds of heating element equipment that need to be cooled, such as: central air conditioning units, air compressors, induction coils of industrial melting furnaces and medium frequency melting furnaces, induction heating furnaces, intermediate frequency power supplies, IGBT power supplies, resist welding machines, laser equipment and high frequency equipment, heat treatment and quenching Circulating cooling of media, molds, generator sets, large hydraulic stations, etc.
Features of Induction Furnace Coil Cooling System
Effective Heat Removal
It is highly efficient in removing heat generated during the induction melting process. The continuous flow of cooling water ensures rapid heat transfer from the coil, preventing overheating and maintaining a stable operating temperature range. This efficient heat removal capability allows for consistent and reliable performance of the induction furnace.
Enhanced Coil Lifespan
The ability of the cooling systems to maintain the coil at the desired temperature range significantly extends its lifespan. By preventing excessive heat buildup, these cooling systems minimize the risk of thermal stress and coil damage. This leads to reduced maintenance and replacement costs, ultimately improving the overall longevity and durability of the coil.
Improved Melting Efficiency
Maintaining a consistent and controlled temperature through the induction furnace coil cooling systems enhances the melting efficiency of the induction furnace. By controlling the cooling rate, the system ensures optimal working conditions for the coil, leading to efficient and uniform melting of the metal charge. This results in improved productivity, reduced energy consumption, and better-quality castings.
Temperature Control and Stability
It offers precise temperature control capabilities. Temperature sensors and control systems continuously monitor the temperature of the cooling water and adjust the flow rate or other parameters as necessary to maintain the desired temperature range. This ensures stable and accurate temperature control, minimizing temperature fluctuations and providing a controlled environment for the induction furnace operation.
Flexibility and Adaptability
Induction furnace coil cooling systems can be designed to suit various induction furnace configurations and requirements. They can be customized based on the specific cooling needs, coil design, and power levels of the furnace. This flexibility allows for easy integration into existing furnace setups or adaptation to different melting applications, making closed water cooling systems a versatile choice for different industrial environments.
Considerations
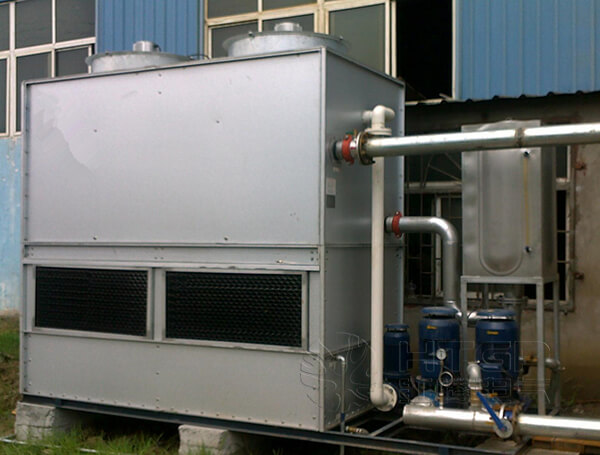
Flow Rate and Pressure
Proper flow rate and pressure of the cooling water are essential for effective heat transfer. The pressure of the cooling water going into the induction furnace coil should be not less than 0.2MPa.
Temperature Control
The system should include temperature sensors and controls to maintain the desired operating temperature range. The inlet and the outlet temperature has a strict standard. The former is not higher than 10℃, and the latter is less than 55℃.
Water Quality
The quality of cooling water, such as its purity, pH, and mineral content, should be considered to prevent corrosion and scaling. Because of the cooling water is isolated with the air, we need to use demineralized water to avoid deteriorate and scale.
Antifreeze
When the temperature is low in winter in the northern region, the circulating water in the closed system will freeze even if the circulating water keeps flowing without heat load. Proper anti-freezing measures must be taken.
Maintenance and Monitoring
Regular maintenance, inspection, and monitoring of the cooling system are crucial to ensure its optimal performance.
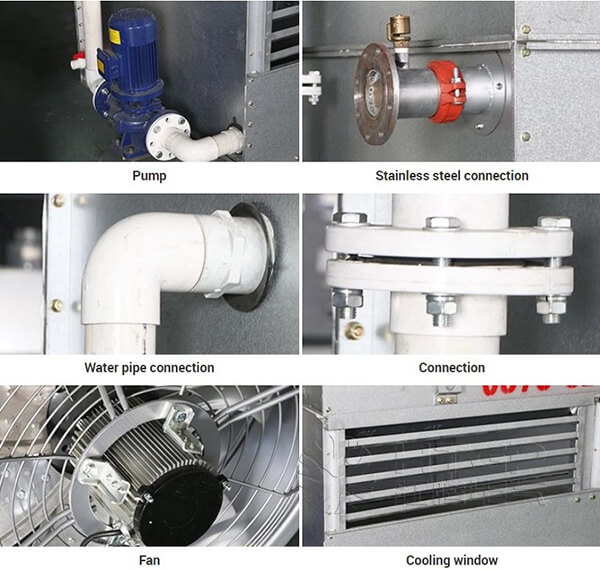
Comparison of Cooling Methods
Water Cooling
The most common method, using water as the cooling medium, offers excellent cooling efficiency but requires proper water quality maintenance.
Air Cooling
In certain applications, air cooling systems can be used as an alternative, although they may have lower cooling efficiency.
Benefits of Effective Coil Cooling Systems
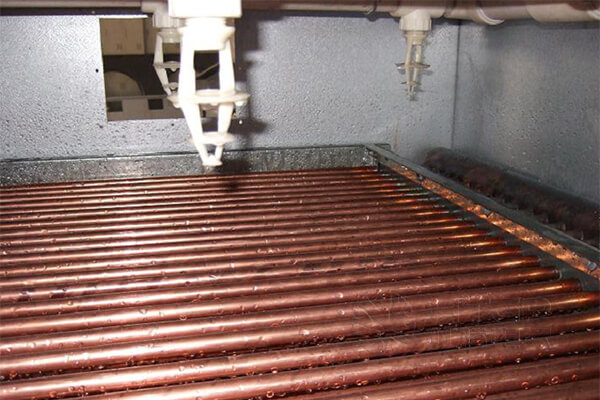
Extended Coil Lifespan
Proper cooling helps prevent overheating and coil damage, leading to a longer lifespan.
Improved Melting Efficiency
Optimal cooling allows for consistent and efficient melting operations.
Energy Efficiency
Well-designed cooling systems can reduce energy consumption by efficiently removing heat.
Conclusion
Induction furnace coil cooling systems are integral to the performance and durability of induction furnaces. By understanding the components, working principles, and features of these systems, operators can make informed decisions regarding their design, maintenance, and operation. Implementing an effective coil cooling system ensures optimal performance, extends the lifespan of the furnace coil, and enhances overall productivity in metal melting operations.