How Is Steel Rebar Made: From Induction Melting Furnace to Steel Rolling Mill
Nowadays, we need a large quantity of steel rebar to build houses, bridges, factories, railways, etc. Do you know how is rebar made? If you have lots of scrap steel or scrap iron, what equipment do you need to produce rebar? In this article, we will introduce you to the whole production process of rebar and the necessary equipment.
Production Process: How Is Rebar Made?
Rebar, short for reinforcing bar, is a type of steel reinforcement commonly used in construction to provide strength and stability to concrete structures such as buildings, bridges, and foundations. There are two types of processes for manufacturing rebar, from scrap steel and from steel billet.
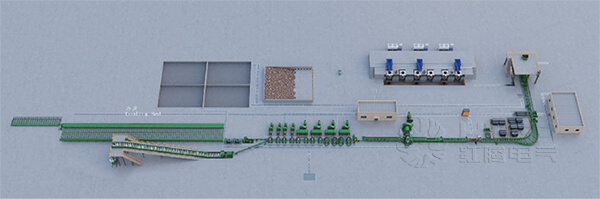
If you want to produce rebar from scrap steel, there are several steps you must take: Heating and melting scrap steel, casting steel billet, and rolling.
Steel Production
Rebar is made from steel, which is primarily composed of iron along with small amounts of carbon and other elements. The first step in manufacturing rebar is the production of steel through one of the following methods: basic oxygen furnace (BOF), electric arc furnace (EAF), or secondary steelmaking.
Generally, we heat and melt the scrap steel in an induction steel melting furnace. The melting point of the steel is about 1500℃, and we need to heat the liquid steel to about 1600℃ to ensure the billet cast in the following process can be more than 1150℃.
Billet Production
Once we get the liquid steel, it is typically cast into large rectangular blocks known as billets. These billets serve as the raw material for manufacturing rebar.
Rolling
The billets pass through a series of rolling mills, which gradually shape them into the desired dimensions. The rolling process involves applying high pressure to the billets, causing them to elongate and reduce in cross-sectional area. The billets are typically rolled multiple times to achieve the desired size and shape.
Ribs and Deformation
To enhance the bonding between the rebar and the surrounding concrete, ribs or deformations are often added to the surface of the rebar. This is typically done by passing the rebar through specially designed ribbing rollers during the rolling process. The ribs provide a larger surface area for the concrete to grip onto, improving the overall strength of the structure.
Cooling
After the rolling process, the rebar is allowed to cool either naturally or through controlled cooling methods. This helps to normalize the steel’s microstructure and enhance its strength.
Cutting and Coiling
Once the rebar has cooled, it is cut into desired lengths using shearing machines. Depending on the requirements, the rebar may also be coiled into large spools or bundles for easy transportation and handling.
Quality Control
Throughout the manufacturing process, various quality control measures are implemented to ensure that the rebar meets the specified standards and requirements. This includes conducting tests for dimensions, mechanical properties, and surface quality.
Necessary Equipment
You may need induction steel melting furnaces, continuous casting machines, rolling mills, and other auxiliary machines to get high-quality rebars.
Induction Steel Melting Furnace
An induction steel melting furnace typically consists of a crucible, an induction coil, a power supply, and a cooling system. The crucible, often made of refractory materials like graphite or clay, holds the steel to be melted. The induction coil, made of copper or other conductive materials, surrounds the crucible and is connected to the power supply. The cooling system helps maintain the temperature of the induction coil.
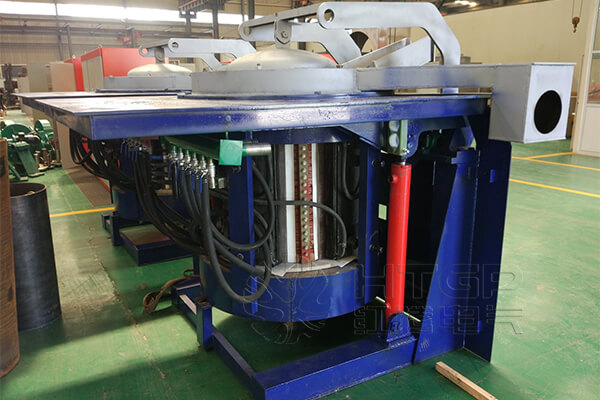
The power supply of an induction furnace produces a high-frequency alternating current that is fed to the induction coil. The frequency of the current is usually in the range of several hundred to a few thousand hertz, depending on the size and capacity of the furnace. The high-frequency current is crucial for efficient induction heating.
Continuous Casting Machine
The construction of a continuous casting machine involves several key components and structural elements. A continuous casting machine usually consists of a mold, a tundish, a withdrawal system, a cooling system, and a control system. While specific designs may vary depending on the type and size of the machine.
As the name shows, the continuous casting machine is to cast steel billet from liquid steel continuously. Thus, the following process can work smoothly. The billet size ranges from 50*50mm to 150*150mm as required and the length is usually 1 –1.5 meters.
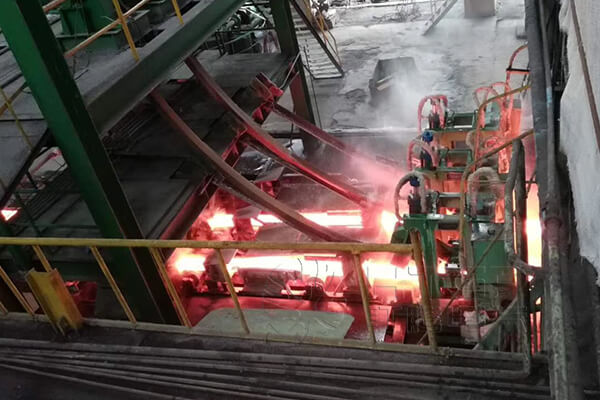
Rolling Mills
To produce steel bars with precise forming and superior performance, we need to use several hot rolling mills. When arranging the rolling mills, we need to consider Compression ratio, pass distribution, reduction amount, steel turning procedure, rolling speed, biting speed, throwing speed, coiling speed, etc.
A roughing rolling mill, also known as a rougher, is a type of rolling mill used in the metal industry to reduce the thickness of metal ingots or slabs in the early stages of the rolling process. Its primary function is to pre-shape the metal and prepare it for subsequent rolling passes in a finishing mill.
An intermediate rolling mill, also known as an intermediate mill or intermediate stands, is a type of rolling mill used in the metal industry to further reduce the thickness of metal coils or billets after they have passed through the roughing mill. Generally, several intermediate rolling mills are positioned between the roughing mill and the finishing mill in a line. The primary function of the intermediate mills is to continue the reduction process and prepare the metal for the final stages of rolling.
Finishing mill or simply a finishing stand, is the final stage in the rolling process of metal products. It is responsible for achieving the desired size, shape, and surface quality of the rolled metal. The finishing mill follows the intermediate rolling mill and is typically the last step in a rolling mill line.
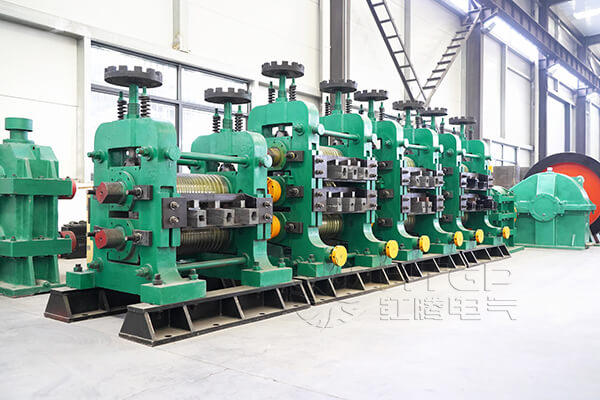
Auxiliary Machines
The equipment mentioned above is necessary. Of course, we need some auxiliary machines to complete the whole process, such as the cutting machines, the coiling machines, the packing machines, the cooling systems, etc.
Conclusion
Now do you know how rebar is made? I believe you do. However, it is important to note that variations in the manufacturing process may exist depending on the specific requirements and standards of different countries and regions. However, the general steps outlined above provide a basic understanding of how rebar is typically made.