Common 1 ton induction melting furnace and electric cabinet
Today, I would like to introduce to you the most common product of our Hongteng. An intermediate frequency induction furnace that can melt 1 ton of metal at a time.
For the smelting of different metals, due to the different proportion of metal, the same 1 ton of metal, its volume is different, so the shape of the melting furnace body is different, the induction coil size is also different. The size is different, the diameter is the same, its coil turns are also different.
When smelting different metals, the furnace is different. The weight of alloy steel, alloy aluminum and alloy copper melting furnace is 1 ton, the melting furnace body is different. With alloy steel as the standard, 1 ton of alloy aluminum smelting furnace body is equivalent to 11 tons of alloy steel furnace body; And 1 ton of alloy copper smelting furnace body is equivalent to 1700Kg alloy steel furnace body.
Each furnace needs to be heated to a different temperature. For example, the melting temperature of 1 ton alloy steel melting furnace is generally 1650 degrees; The melting temperature of 1 ton alloy aluminum melting furnace is generally 800 degrees; The melting temperature of 1 ton alloy copper smelting furnace is generally 1200 degrees.
In terms of melting a furnace of metal in an hour, the smelting power of a 1 ton furnace is still different. The melting power of 1 ton alloy steel melting furnace is 350Kw; The smelting power of 1 ton alloy aluminum smelting furnace is 250Kw; And the smelting power of 1 ton alloy copper smelting furnace is 300Kw.
To sum up, when we say 1 ton smelting furnace, first of all, we must distinguish what is the material of smelting metal, in order to determine the real 1 ton smelting furnace, otherwise there will be 1 ton smelting furnace smelting effect is very different, resulting in understanding errors and can not be applied or use up to reach the design capacity.
The solution we often design for users is a set of power supply cabinet with two furnace bodies.
One furnace body is connected to the power supply, and the other one is temporarily not in use. This method is adopted to prepare a spare furnace body for the production line. If a furnace body fails and cannot be repaired in a short time, we at least have a spare plan B available to maintain the capacity as much as possible.
Or two furnace bodies are connected to the power supply, a furnace body fixed melting, another furnace body fixed insulation. This method is suitable for longer pouring time. The molten steel needs to be kept at temperature in the furnace for a period of time, so the method of one melting and one holding is adopted, so that both furnace bodies can be fully utilized.
Of course, these schemes are only our suggestions, and the specific configuration should be done according to the actual production situation of users.
This is the introduction of induction furnace shared by editor Luoyang Hongteng. Welcome to pay attention to us for more information about induction furnace.
Video of the use process of the furnace
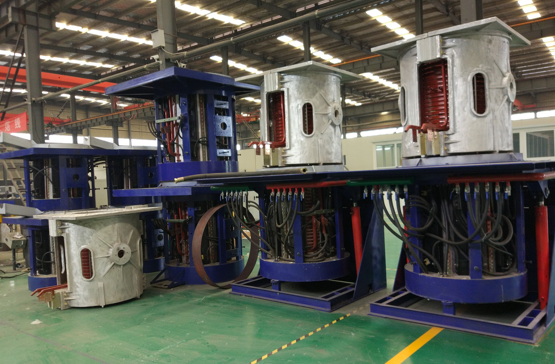