How Do Induction Foundry Furnaces Enhance Productivity and Cost Efficiency?
Induction foundry furnaces are specialized equipment used in the manufacturing industry for melting and heating metal alloys. These furnaces utilize electromagnetic induction to generate heat within the metal material, allowing for precise temperature control and efficient melting processes.
Benefits of Induction Foundry Furnaces
Induction foundry furnaces are crucial components in the manufacturing industry, offering several benefits that contribute to enhancing productivity and cost efficiency.
- 1. Increase efficiency in heating and melting metal alloys
- 2. Consistent and precise temperature control
- 3. Reduce energy consumption compared to traditional furnaces
- 4. Melt metals at a faster rate to meet production targets more efficiently
- 5. Too high reliability and durability to maintain frequently and reduced downtime
Importance of Induction Foundry Furnaces in Manufacturing Industry
Induction foundry furnaces are widely used in foundries, metal fabrication facilities, and other manufacturing operations that require the melting and shaping of metal for various applications.
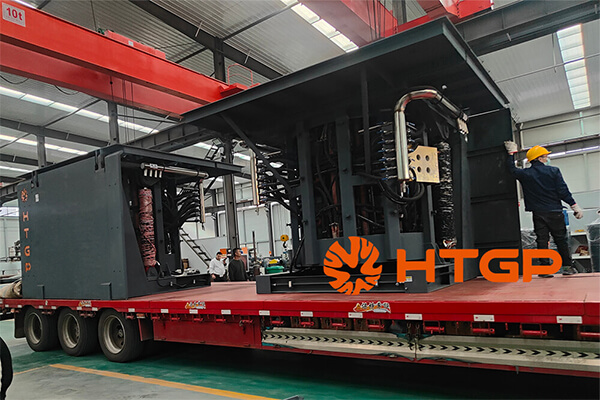
Efficiency
Induction foundry furnaces offer high efficiency in the heating and melting of metal alloys. The electromagnetic induction process allows for rapid and uniform heating, leading to quicker melting times and increased productivity in manufacturing operations.
Precision
These furnaces provide precise temperature control, ensuring that the metal reaches the desired melting point consistently. This level of control is crucial for maintaining the quality and integrity of the metal during the melting process.
Energy Efficiency
Compared to traditional furnaces, induction foundry furnaces are more energy-efficient. They consume less power and produce less waste heat, resulting in cost savings and reduced environmental impact for manufacturing facilities.
Versatility
Induction foundry furnaces are versatile equipment that can be used for melting a wide range of metal alloys, making them suitable for various applications in industries such as automotive, aerospace, and construction.
Measures to Enhance the Productivity and Cost Efficiency
Here is an overview of how induction foundry furnaces play a significant role in optimizing manufacturing processes.
Optimize Furnace Design and Process Parameters
The design of the induction casting furnace should take into account the characteristics of the material, the needs of the melting and casting process. Optimizing the furnace structure and rationally laying out components such as sensors, furnaces, and power supplies can improve energy transfer efficiency and reduce energy loss. At the same time, the appropriate melting temperature and melting speed should be selected according to the properties of the material to ensure that the metal or alloy can be melted evenly and reduce melting time and energy consumption.
Introducing Automation and Intelligent Technology
By introducing automation and intelligent technology, remote monitoring and precise control of casting furnaces can be achieved. For example, sensors and control systems are used to monitor parameters such as temperature and pressure in the furnace in real time, and automatic adjustment of power and frequency ensures the stability and efficiency of the smelting process. In addition, automated equipment such as robots can also be used to complete tasks such as delivering and taking out materials, reducing labor costs and improving production efficiency.
Strengthen Energy Management and Energy-Saving Measures
Induction casting furnaces consume a large amount of electricity during operation, so it is crucial to strengthen energy management and take energy-saving measures. Power consumption can be reduced by optimizing the power system, improving power efficiency, and using energy-saving sensors. In addition, waste heat can be rationally utilized and cooling water consumption can be reduced to further reduce operating costs.
Regular Maintenance and Upkeep
Maintenance and upkeep of your induction casting furnace is critical to keeping it running efficiently. Regularly inspect and repair the furnace body, sensor, power supply and other components to ensure that they are in good working condition. At the same time, keeping the furnace clean to prevent impurities and oxides from contaminating the metal or alloy will help improve product quality and reduce the scrap rate.
Conclusion
Induction foundry furnaces play a vital role in the manufacturing industry by providing efficient, precise, and cost-effective solutions for melting and heating metal alloys. Their importance in enhancing productivity, ensuring product quality, and driving cost efficiency makes them essential equipment for modern manufacturing operations.