Induction Heater for Forging vs. Traditional Heater for Forging
In the realm of forging, the choice between an induction heater and a traditional Heater can significantly impact the efficiency, quality, and overall performance of the heating process. Let’s delve deeper into the key factors that differentiate these two heating methods.
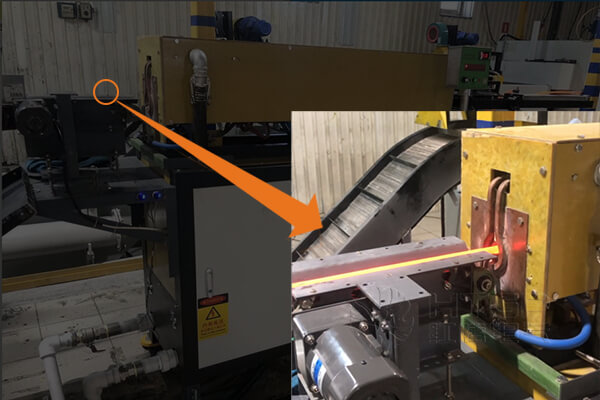
Efficiency and Precision
Induction heating offers superior efficiency by directly heating the metal part, reducing heat loss and energy consumption.
The precise control of temperature and heating patterns with induction heating furnaces results in better metallurgical outcomes compared to traditional heaters.
Speed and Productivity
Induction heating excels in rapid heating cycles, leading to shorter processing times and increased productivity in forging operations.
Traditional heaters may lag in heating speed, potentially causing delays in production schedules.
Energy Consumption and Cost Savings
Induction heating’s energy-efficient design translates to reduced electricity usage and lower operating costs over time.
Traditional heaters, such as gas or oil-fired systems, may incur higher energy expenses and maintenance costs.
Safety and Environmental Impact
Induction heating offers a safer working environment by eliminating open flames and reducing the risk of accidents or injuries.
Traditional heaters can pose safety hazards due to open flames, fumes, and potential environmental pollution.
Material Compatibility and Maintenance
Induction heating is suitable for various materials, including ferrous and non-ferrous metals, with minimal material wastage during the heating process.
Traditional heaters may require more frequent maintenance, such as burner cleaning or part replacement, impacting operational downtime and costs.
Cost Analysis and Long-Term Benefits
Conducting a comprehensive cost analysis can help businesses evaluate the initial investment and long-term benefits of switching to induction heating for forging applications.
Considering factors like energy efficiency, maintenance costs, and production output can provide insights into the overall cost-effectiveness of each heating method.
Real-World Applications and Case Studies
Showcase real-life examples of companies that have successfully integrated induction heating into their forging processes, highlighting the tangible benefits in terms of quality, efficiency, and cost savings.
By exploring case studies, readers can gain practical insights into the transformative impact of adopting induction heating technology in the forging industry.
By weighing these critical factors, businesses can make informed decisions when choosing between the induction heater and the traditional Heater for their forging operations, ultimately optimizing performance and driving innovation in the ever-evolving field of metalworking.