Induction Coils and Industrial Metal Furnace Power
We, Hongteng, are a company that produces industrial furnaces. Today, I will share with you some knowledge about industrial metal furnaces.
When the industrial furnace is working, the power is a problem that everyone is concerned about, so how to improve the power of the intermediate frequency induction furnace?
The coil is the key to converting electrical energy into heat, so the design of the coil is very important.
The advanced coil design should be based on the actual use of the induction furnace, according to the principle of electromagnetic field, through the optimization calculation of the computer industry software to determine a good plan, using the new coil anti-parallel winding technology, better gather the magnetic field, improve the magnetic field stirring force, The error between the design power of the induction coil and the actual operating power is not more than 5%.
We can increase the wall thickness of the induction coil.
Thick-walled induction coils will provide more smelting energy, and thick-walled induction coils have larger current-carrying cross-sections than induction coils with other cross-sections, so the coil resistance is low and more energy can be used for smelting.
And because the thickness of the surrounding pipe wall is uniform, its strength is higher than that of the coil structure with uneven pipe wall and thinner side pipe wall. That is to say, the coil of this structure is less prone to damage caused by arcing and expansion.
Increase the induction coil turn spacing. The open space between turns of the induction coil increases the electrical rate and reduces water vapor.
Such a design can not only improve the current-carrying rate of the coil, but also make the water vapor in the furnace lining material easy to volatilize. A common problem in furnaces with gapless induction coils is that the coils are often affected by the magnetic field of the adjacent coils, causing an increase in impedance from the surface.
The coil is the heart of the induction furnace. The induction coil is powered by an intermediate frequency power supply. Under the action of the intermediate frequency power supply and current, a strong magnetic field is generated.
The design of the induction coil is also the top priority of the energy saving of the intermediate frequency furnace. If the density of the induction coil of the intermediate frequency furnace is selected, the power loss will increase, and the electrical efficiency of the induction coil of the intermediate frequency furnace will decrease. Therefore, the section size of the pure copper tube of the induction coil of the intermediate frequency furnace is determined by The number of turns of the induction coil and the geometry of the induction furnace.
In this way, the inductor coil of the intermediate frequency furnace largely determines the energy-saving effect of the energy-saving intermediate frequency furnace.
The design of an industrial furnace is all-round, and it is necessary to consider the power effect from all angles of manufacture, use, and purchase of a suitable industrial furnace.
This is what we share today. If you are interested, you can follow Luoyang Hongteng to learn more about industrial furnaces.
Video of the use process of the furnace
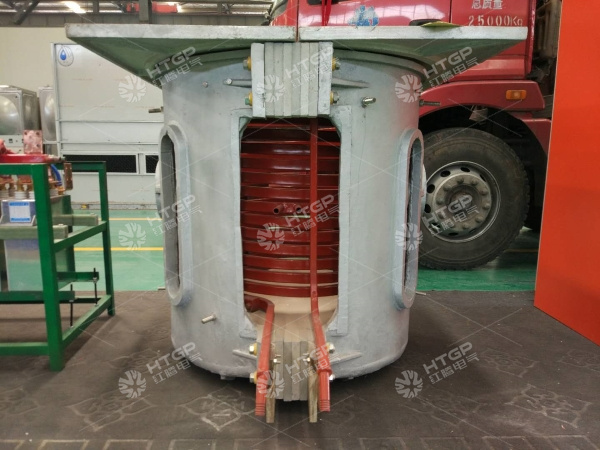