Technological Requirements of Continuous Casting and Rolling Production Line
The definition of continuous casting and rolling: the high-temperature defect-free billet produced by the continuous casting machine does not need to be cleaned and reheated (but it needs to be soaked for a short time and heat preservation treatment), and it is directly rolled into a product so that the “casting” and “rolling”. The technological process that is directly connected to a production line is called continuous casting and rolling.
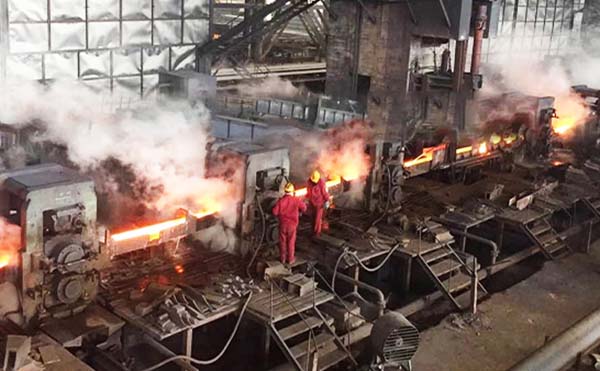
Requirements for CCM in Continuous Casting and Rolling
The continuous casting machine should be suitable for the whole process of high-temperature molten steel from liquid to liquid to solid and then to solid.
The CCM should be of high-temperature resistance, fatigue resistance performance, and sufficient strength.
It has high manufacturing and installation precision, easy maintenance and quick replacement, sufficient cooling and good lubrication, etc.
A Method for Compact Coupling of Continuous Casting and Rolling
Continuous casting is also hot charging and direct rolling. The continuous casting and hot charging process refers to the method in that the steel produced by the continuous casting machine is not cooled, but is involved in the heating furnace to be heated in a hot state, and then rolled. The continuous casting bad direct rolling process means that the high-temperature cast bad from the casting machine is directly sent to the rolling mill for rolling without heating or only slightly supplementary heating on the edges.
Advantages of Continuous Casting and Rolling
Cost Efficiency
Continuous casting and rolling eliminate the need for intermediate steps such as reheating, which reduces energy consumption and production costs.
Improved Quality
Continuous casting and rolling can produce high-quality products with consistent properties. The process allows for precise control of the cooling rate, resulting in a fine-grained microstructure and improved mechanical properties.
Increased Productivity
Continuous casting and rolling can produce a large volume of products in a short amount of time, which increases productivity and reduces lead times.
Versatility
Continuous casting and rolling can be used to produce a wide range of products, including flat and long steel products, as well as specialty steel products with specific properties.
Reduced waste: Continuous casting and rolling can reduce waste by producing products to exact specifications, minimizing material scrap, and improving yield.
Limiting Factor for High Pulling Speed
Limitation of Pulling Force
The pulling force required to draw the solidifying steel through the mold can be calculated as the product of the cross-sectional area of the steel shell and the surface tension of the steel. As the casting speed increases, the cross-sectional area of the steel shell decreases, which increases the pulling force required to maintain a constant casting speed. This can lead to higher tensile stresses in the steel shell, which can cause it to break or crack.
Cooling Conditions
In addition to the pulling force, the cooling conditions in the mold can also affect the strength of the solidifying steel shell. Rapid cooling can cause thermal gradients to develop in the steel shell, which can lead to the formation of cracks and other defects. To mitigate these issues, mold powders and other coatings can be applied to the mold surface to improve heat transfer and reduce thermal stresses.
The Flow of Molten Steel
The flow of molten steel through the mold can also affect the strength of the solidifying steel shell. Non-uniform flow patterns can cause uneven solidification and the formation of defects such as surface cracks and internal voids. Techniques such as electromagnetic stirring can be used to improve the flow of molten steel through the mold and reduce the formation of defects.
Cooling Method in the Secondary Cooling Zone
Dry cooling;
Water spray cooling;
Water-air spray cooling (the best)
Inverted Taper
In order to reduce the air gap, and accelerate the heat transfer of molten steel and the growth of bad shells, the lower section of the crystallizer is usually smaller than the upper section. If the reverse taper is too small, the bad shell will break away from the copper wall prematurely to form an air gap, which will reduce the cooling effect, or cause the bad shell thickness of the crystallizer to be insufficient, resulting in leakage accidents; Excessive extrusion force will accelerate the wear of the copper wall.
The Requirements for Crystallizer
Simple structure and lightweight;
Good guiding and water cooling conditions;
It should reciprocate up and down and add lubricant;
The crystallizer has sufficient rigidity so as not to affect the casting quality.