Using induction furnace should pay attention to: furnace lining and oven
In the use of melting furnace, slag erosion is a common form of refractory damage. In fact, more than 59% of liner material damage is caused by slag erosion.
In the process of melting, the furnace wall should be subjected to the impact force of the metal charge, the static pressure of the metal liquid, the electromagnetic stirring of the metal liquid movement, the thermal stress and other effects, which will affect the service life of the melting furnace lining.
Therefore, the lining material should have a certain high temperature strength, no cracking and anti-erosion under the action of a variety of forces.
In the melting furnace, the temperature difference between the inside and outside of the furnace wall is very large. About 10% ~ 15% of the heat is lost through the furnace wall. In order to reduce the heat loss and improve the thermal efficiency, the lining material should have low thermal conductivity.
At the same time, the lining material should have a low conductivity, can not contain magnetic induction, especially the lining knotting process is not allowed to metal or strong conductivity substances in it.
When the melting furnace is working, the temperature of liquid steel can reach 1700℃ or above, and the temperature of liquid iron can reach 1500℃ or above. Therefore, the lining material should have good refractories, and the lining material should be selected to meet the melting temperature or withstand partial and frequent high temperature according to the smelting material.
Melting furnace lining should be under the contact of high temperature metal liquid, high vacuum, high (acid) alkaline slag, should not decompose reduction, do not participate in chemical reaction, has good chemical stability.
Oven must add a certain amount of charge, about 70% of the height of the furnace, to ensure the uniformity of temperature rise and fall.
Oven to take low power, slow heating, at the same time to power through cooling water. At the initial stage of the oven, the heating rate is 100℃/h and rises evenly until 800-900℃.
Clean and rust-free return material is selected to reduce slag, of which large material should be installed around the wall of the crucible, and small pieces of material should be added in the center of the furnace bottom.
The temperature of liquid iron should be about 50℃ higher than the working temperature, and keep 1-2h, so that the furnace lining is uniformly sintered. The whole melting time of the first furnace is about 2-3 times of the normal melting time.
After melting the first furnace, the sintering layer of the crucible is still very thin, and the sintering process can be completed only after continuous melting for 2-3 more furnaces.
If the sintering temperature is too low and the time is not enough, the lining will break after cooling.
This is our knowledge sharing today, about the electric furnace lining oven technology. I hope I can help you.
Welcome to pay attention to us for more information about induction furnace.
Video of the use process of the furnace
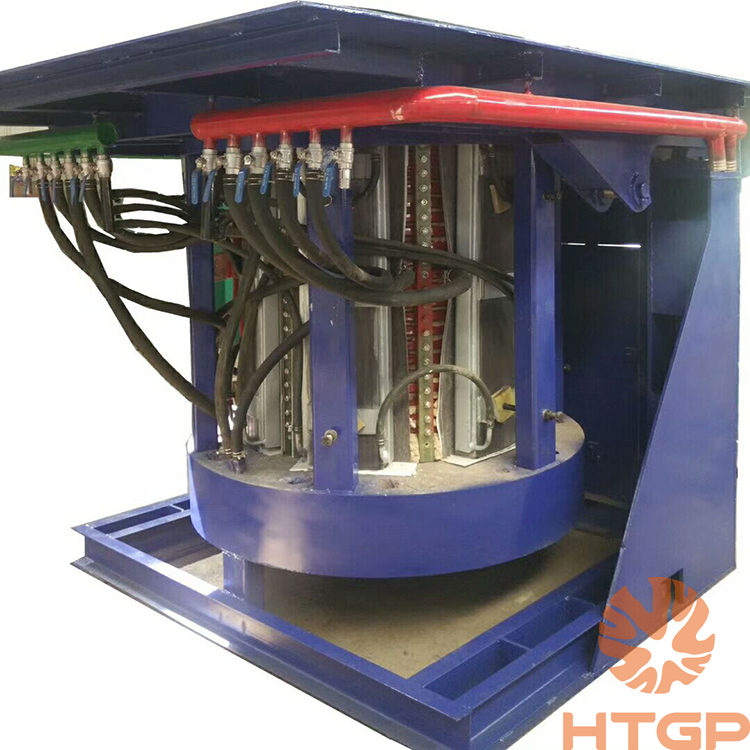