Aluminum Ingot Casting Continuous Production Line
Aluminum ingot casting is a manufacturing process used to produce aluminum products of various shapes and sizes. The process involves melting aluminum ingots, which are cylindrical blocks of aluminum, and pouring the liquid aluminum into a mold. Once the aluminum has cooled and solidified, the mold is removed, and the cast aluminum product is ready for further processes such as machining, welding, or finishing.
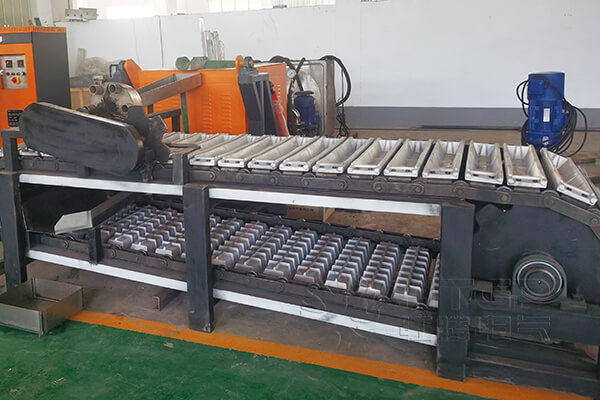
There are different techniques for aluminum ingot casting, including continuous casting, sand casting, die casting, and permanent mold casting. The choice of casting technique depends on several factors, including the complexity of the product, the quantity required, and the budget available for the project.
Several Advantages of Continuous Aluminum Ingot Casting
Quick production: Aluminum ingot casting is fast and efficient, and can produce large quantities of aluminum products quickly;
Low cost: Aluminum ingot casting is generally less expensive than other casting methods, such as sand casting or die casting, making it a cost-effective option for many manufacturers;
Versatile: Aluminum ingot casting can be used to produce a wide range of products, from simple parts to complex designs, and can be used with a variety of other materials, such as plastics, to create composite products;
Good structural integrity: Aluminum ingot casting produces high-quality products with good structural integrity, which can be used in a variety of demanding applications;
Recyclable: Aluminum is a highly recyclable material, and ingot casting allows scrap aluminum to be efficiently recycled and reused in new products, making it an environmentally-friendly option;
Lightweight: Aluminum is a lightweight material, making it ideal for applications where weight is a concern, such as in the automotive or aerospace industries.
How Much Does An Aluminum Ingot Weigh?
The weight of an aluminum ingot can vary depending on the manufacturing process and the size of the ingot. However, standard aluminum ingots typically weigh around 50 pounds or 22.7 kilograms.
Aluminum ingots used for manufacturing purposes are typically cast into rectangular shapes, measuring approximately 20 inches by 10 inches by 6 inches (50 cm x 25 cm x 15 cm). These ingots are called “pigs” or “bars,” and they weigh around 50 pounds.
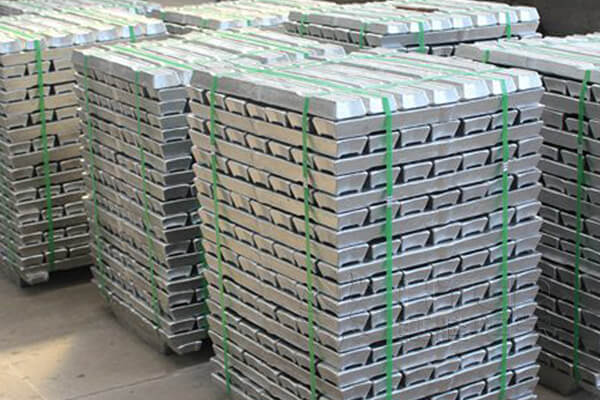
Smaller ingots, called “buttons,” are also used in some manufacturing processes, such as those used to produce semiconductors, and these can weigh as little as a few grams.
It’s worth noting that some manufacturers produce aluminum ingots with unique shapes and sizes, tailored to their specific manufacturing processes. In these cases, the weight of the ingot will depend on the size and shape of the ingot itself.
Continuous Aluminum Ingot Casting Production Line Capacity
The capacity of a continuous aluminum ingot casting production line varies depending on several factors such as the size of the ingots, the speed of production, and the number of casting stations. However, typical production capacities for continuous aluminum ingot casting production lines range from 10,000 to 30,000 tons per year.
The production capacity of a continuous aluminum ingot casting production line can be increased by adding more casting stations, increasing the speed of production, and enhancing the efficiency of the equipment. Moreover, automating the production line can increase production capacity and reduce labor costs.
It’s worth noting that the production capacity of a continuous aluminum ingot casting production line is also affected by the quality of the inputs, such as the purity of the aluminum alloy and the quality of the scrap feedstock. Higher-quality inputs typically result in higher-quality output and can increase the overall production capacity of the line.
Ultimately, the actual production capacity of a continuous aluminum ingot casting production line will depend on many individual factors and can vary widely from one facility to another.
Applications of Aluminum Ingots
Aluminum ingots are used to produce a wide range of aluminum products for various industries. Here are some common applications of aluminum ingots:
Manufacturing: Aluminum ingots are used to produce a variety of aluminum products such as alloy wheels, engine blocks, aerospace components, and construction materials;
Transportation: Aluminum ingots are used to produce parts for transportation equipment, including cars, trucks, and aircraft. Aluminum’s lightweight and high-strength properties make it an ideal material for transportation applications, where weight reduction is important for improving fuel efficiency;
Electronics: Aluminum ingots are used to produce components for electronics such as mobile phones, laptops, and televisions;
Packaging: Aluminum ingots are used to produce aluminum foil, a popular packaging material used for food and beverages;
Construction: Aluminum ingots are used to produce various construction materials, including window frames, roofing materials, and siding. Aluminum’s corrosion resistance and durability make it suitable for use in harsh outdoor environments;
Power generation: Aluminum ingots are used to produce components for renewable energy technologies, such as wind turbines and solar panels.
Hongteng aluminum ingot casting production line is mainly used for the automatic casting of aluminum, copper, and other non-ferrous metals. The capacity can reach up to 10 Ton per hour. If you need this production line, please do not hesitate to get in touch with us.