How to Choose the Induction Furnace in the Foundry?
With the rapid development of solid-state medium-frequency power supply technology, medium-frequency induction furnaces are increasingly widely used in modern foundry workshops. So, how to choose an induction furnace for a foundry workshop? What is the relationship between the capacity and power of the electric furnace and the process requirements? What is the relationship between the type of power supply, the configuration of power supply and electric furnace, etc., and the process requirements? In addition, what are the system’s functional integrity, safety, advancement, economy, and adaptability to environmental protection that need to be considered when selecting an electric furnace? This article will introduce it to you in detail.
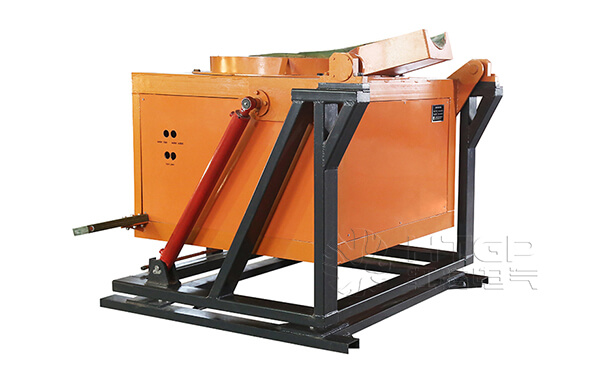
Determination of Electric Furnace Capacity and Power
The determination of the capacity of the electric furnace must consider many process factors, but basically, it should meet two conditions. One is to meet the pouring weight requirement of the largest casting, and the other is to be consistent with the demand for molten iron in the process. Due to the relatively large power density configuration of the intermediate frequency electric furnace, when its configuration power density is greater than 600 kw/t, its melting capacity can basically achieve a melting time of less than one hour per heat.
Choice of Power Supply Type
There are two main types of intermediate frequency power supplies: solid power supplies with parallel inverter circuits and solid power supplies with series inverter circuits.
In my country’s foundry industry, the intermediate frequency induction furnace that is used to configure the SCR full-bridge parallel inverter solid power supply is commonly known as the intermediate frequency furnace. The intermediate frequency induction furnace configured with (IGBT) or (SCR) half-bridge inverter solid power supply is commonly known as a frequency conversion furnace.
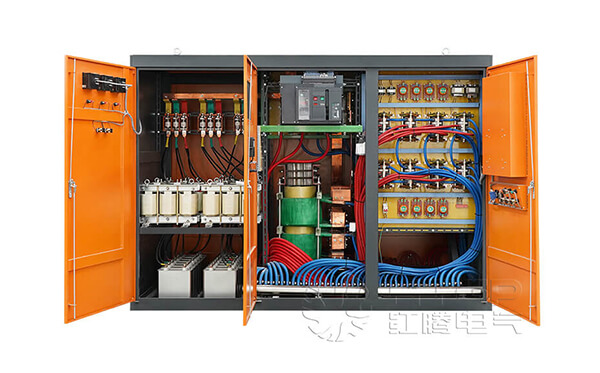
Configuration of Medium Frequency Power Supply and Electric Furnace
The batch melting method using a medium frequency centerless induction furnace can keep the output power of the power supply at the maximum load level from the moment the charge is heated to before pouring. However, during the subsequent pouring operation cycle and other non-productive operation periods (such as slag removal, sampling, waiting for laboratory results, etc.), the system has no power output or only a small amount of power output to maintain a certain pouring temperature.
Relationship between Melting Rate and Productivity of Electric Furnace
Furnace melting capacity data provided by electric furnace manufacturers on catalogs or technical specifications is the melting rate. The melting rate of the electric furnace is the characteristic of the electric furnace itself. It is related to the power of the electric furnace and the type of power supply and has nothing to do with the production system. The productivity of the electric furnace is not only related to the melting rate performance of the electric furnace itself but also related to the melting operation system. Usually, there is a certain no-load auxiliary time in the melting operation cycle, such as: feeding, skimming, sampling and testing, waiting for test results (related to test methods), waiting for pouring, etc. The existence of these idle auxiliary times reduces the power input of the power supply, that is, reduces the melting capacity of the electric furnace.
Evaluation of Various Functions of the System When Selecting an Electric Furnace
As an important melting equipment in the foundry, the investment of the induction furnace occupies a large proportion of the total investment of the foundry. Therefore, the selection of the electric furnace system should be combined with the investment scale of the foundry itself in addition to the various factors that need to be considered above. Technical advancement, management level, and other backgrounds make a comprehensive analysis and evaluation of the selected electric furnace system’s safety, advancement, economy, adaptability to environmental protection, and other system functions.
System Security
The complete mechanical protection functions of the system should include the use of a closed cooling water circulation system, monitoring and alarming of cooling water temperature and flow, the setting of emergency cooling water tanks and pipelines, safety measures for the hydraulic system, steel for the furnace body Frame structural solidity. The complete electrical protection functions of the system include a fully functional and reliable digital control panel and fault self-diagnosis function, furnace lining detection (or furnace leakage detection) function, reliable cooling measures for power supply (including capacitors, etc.), etc.
The Advanced Nature of the System
It should match the advanced level of equipment and management level background of the entire foundry. Adopting the intermediate frequency power supply of the fully digital control system will greatly improve the stability and reliability of the operation (including furnace life and melting operation) of the electric furnace system. In addition, in recent years, the power-sharing power supply system (commonly known as the one-to-two electric furnace system), the remote control system of the power supply, the automatic control and management system of the computerized melting process of the electric furnace, the rapid ejection mechanism of the old furnace lining, and the molten iron Advanced devices such as the automatic weighing system and the automatic furnace lining oven control system have also greatly improved the operational stability and reliability of the electric furnace system, reflecting the advancement of the technology and management level of the casting workshop, and also providing a basis for the quality management system of casting production.
System Economics
The relationship between the higher one-time investment in selecting an advanced electric furnace system and the system’s lower daily operation and maintenance costs and increased productivity should be comprehensively and reasonably evaluated.
Environmental Improvement
Most modern casting workshops have relatively large production capacity, so the power of the electric furnace is also relatively large, which may cause high-order harmonic pollution to the power grid.
Conclusion
Whether the selection of the medium frequency induction furnace is reasonable is one of the main indicators to test the success or failure of the casting workshop design. Through this article’s introduction to the selection of induction furnaces in foundry workshops, I hope to have some references for the selection of induction furnaces in foundry workshops.