Using medium frequency induction furnace environment and controlling metal melting quality
Induction furnace in the process of use, the temperature and humidity of the surrounding environment also have an impact on it.
If the environment exceeds the standard, light will affect the working efficiency of medium frequency furnace, and serious will lead to some fault problems of electric furnace. Today, Red Teng editor will give you an introduction to the working environment suitable for induction furnace.
The altitude environment of the equipment should not be too high, preferably below 1000 meters above sea level. The best working environment temperature can be in the range of -10℃~40℃.
Under the standard of 25℃, the relative humidity of the surrounding environment should not exceed 90%.
There should be no conductive dust, explosive gas or corrosive gas that can seriously damage metal and insulation around the furnace body, so as to avoid equipment damage or personnel injury.
The fluctuation of three-phase power supply is not greater than ±5%. If the fluctuation is large, it is easy to cause the electric furnace failure, and there is a certain risk.
About the electric furnace at work, melting process of quality control problems, to share with you.
Heat preservation of liquid iron: Heat preservation of liquid iron at high temperature will cause temperature changes, elemental burning, dissolved gas and the state change of liquid iron itself. Therefore, if a long time of insulation is needed, the temperature of insulation should be reduced as far as possible. For example, a small amount of clean and dry return charge can be added to cool down, and the surface of liquid iron is covered with glass and other materials.
Liquid iron composition selection: the same furnace liquid iron to cast several castings, as far as possible in accordance with the batch of the largest casting, or the most important casting ingredients, in the process of pouring liquid steel, the carbon content in the furnace will continue to reduce, can consider adding inoculant first adjustment, and then consider the use of carburizing agent.
Change of liquid iron quality: if there is residual ductile iron liquid iron in the furnace, if you want to melt gray iron liquid iron, if there is more liquid iron, it is better to heat up to 1550℃, and hold heat for a period of time, otherwise there will be a lot of messy graphite blocks in the casting organization, affecting the casting performance.
The oxidation problem of liquid iron: because the charge is not clean or the smelting process is not well controlled, it will lead to the serious oxidation of liquid iron and affect the casting quality problems. Therefore, we should try to choose clean and clean charge, and then we can consider the use of silicon carbide, silicon calcium alloy to deoxidize, and then appropriate temperature and insulation.
This is our share today on the use of medium frequency induction furnace environment and metal smelting quality control. I hope I can help you.
Welcome to pay attention to our Luoyang Hongteng, you can learn more about induction furnace and metal smelting knowledge.
Video of the use process of the furnace
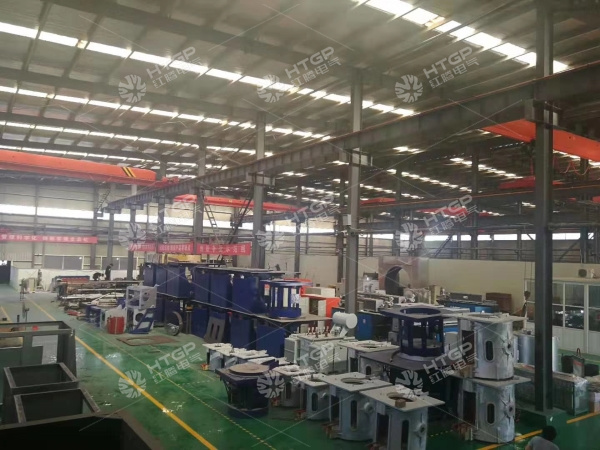